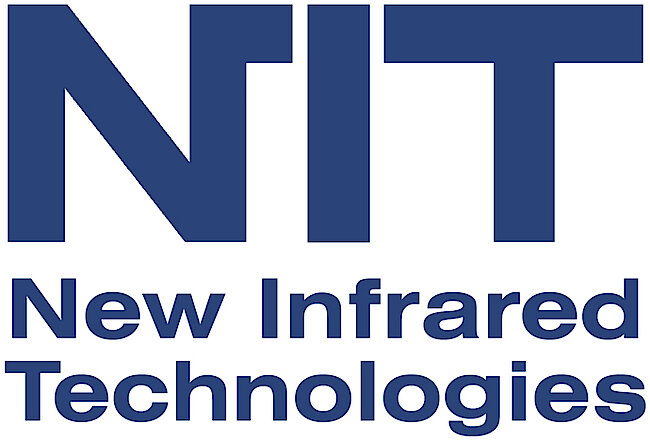
Get to know the consortium members of the CLASCO project. A universal and digitised laser-based post-processing method for the production of functionalised parts with complex shapes is being developed in the EU-funded CLASCO project. 12 international project partners from science, industry, research and application are united in the CLASCO project. The project is coordinated by the Technical University of Dresden. In our exclusive interview series, the CLASCO project consortium members introduce themselves in the areas of CLASCO Machine, Optics, Process Monitoring, Sample Preparation through Additive Manufacturing, Artificial Intelligence, Strategy and Business Model as well as Circularity and Sustainability.
Get to know the CLASCO project consortium member in the area of Process Monitoring:
NIT – New Infrared Technologies
1. What experience do you bring to the CLASCO project, in particular your expertise in developing solutions for real-time monitoring and intelligent control of laser-based industrial processes in an industrial environment?
During the last years NIT has successfully developed and commercialized several systems and solutions for monitoring and controlling in real time industrial laser based processes based in its unique IR technology. In CLASCO project NIT will bring its expertise further improving the optics and electronics of their cameras and developing advanced signal treatment algorithms with the final objective of advancing towards fully automation of industrial laser based processes.
2. The consortium partner nLight is also a specialist in the field of sensor technology for process monitoring. What is the difference between your expertise and nLight?
nLIght develops excellent sensors and solutions for process monitoring. However – n Light technology relies on different principles and sensors than NIT. The systems developed by NIT are based on analyzing IR images captured at high frame rates.
3. What innovative sensor technique is being used in the CLASCO project by your company to assess the quality and homogeneity of the surface structures produced?
The heart of the monitor system developed in CLASCO will be an innovative IR sensor. NIT IR sensor technology is unique. The image sensors manufactured by the company combine three characteristics in one device: they are sensitive in a wide spectral range (1-5 microns), they do not need cooling and they are extremely fast (able to capture up to 4000 frame per seconds). All allows to observe the dynamic and the shape of the melt pool in real time.
4. How does your sensor improve the overall quality and homogeneity of the surface functionalisation produced by the CLASCO Machine?
In the frame of CLASCO, they will be improved different industrial laser based technologies for surface texturing, AM etc. Laser is an excellent tool for many industrial applications. However its nature, most of time based on applying very high density of power, involve complex physics and non linear mechanisms. When it is the case real time/in line monitoring and controlling systems are mandatory for assuring reliable and repetitive industrial processes. The IR sensors manufactured by NIT will help to improve the quality and yield of laser texturing processes and will be a key enabler for advancing towards fully automation.
Thank you to NIT for the information.