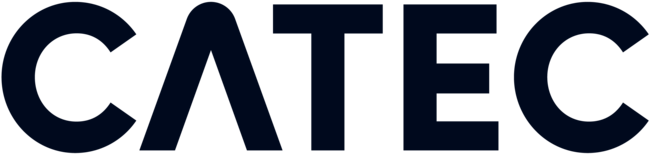
CLASCO project – A universal and digitised laser-based post-processing method for the production of functionalised parts with complex shapes is being developed in the EU-funded CLASCO project. 12 international project partners from science, industry, research and application are united in the CLASCO project. The project is coordinated by the Technical University of Dresden. In our exclusive interview series, the CLASCO project partners introduce themselves in the areas of CLASCO Machine, Optics, Process Monitoring, Sample Preparation through Additive Manufacturing, Artificial Intelligence, Strategy and Business Model as well as Circularity and Sustainability.
Get to know the CLASCO project consortium member in the area of Sample Preparation by Additive Manufacturing:
1. How does CATEC's experience in the development of additive manufactured components for aerospace applications fit with the objectives of the CLASCO project, particularly given the focus on fully digitised laser-based additive manufacturing methods?
CATEC has demonstrated expertise over the last twelve years in the development of additively manufactured aerospace components, where several dozens of parts have been qualified which are flying in space missions and aircrafts. With the aim of improving the performance of the material and, therefore, of aerospace components through laser technologies where the functionalization of the surface is one of the keys, the adoption of AM technologies in the aerospace sector is promoted.
2. How are you working with CLASCO’s Use Case Consortium members DePuy Synthes, CTI and Airbus to support their specific applications?
Yes, we do. As end-users, CATEC is working especially closely with these partners. In the medical sector, with DePuy Synthes we have collaborated closely in the development of a common manufacturing and testing plan for the titanium alloys Ti6Al4V and aluminum Al-Mg-Sc (Scalmalloy®). On the other hand, for the aerospace sector together with the CLASCO members Airbus and CTI, we are working on the optimization of the selected demonstrators to develop a common strategy of calculation and design specifically for AM technologies.
3. From theory to practice: What additive-manufactured samples made by CATEC will support the CLASCO Machine in its development?
In the early stages of the development of CLASCO machine, samples for evaluating the effect of the laser treatment will be crucial, where the surface properties are evaluated as, microstructure, surface roughness, as well as hydrophobic and high friction properties between others. Furthermore, the final Uses Cases and their treatment by laser technologies using the CLASCO machine are very important when such innovative geometries will be treated. Aspects such as accessibility on specific surfaces should be addressed to improve the component's performance, demonstrating the potential for its future industrialization.
4. CATEC is experienced in interdisciplinary cooperation between international partners in the context of large-scale projects. What expertise do you bring to the table? Do you see new challenges for yourself in the CLASCO project?
As a team, we will bring our experience in using and applying PBF-L/M (Powder Bed Fusion-Laser/Metal ) technologies in the aerospace sector, as well as the requirements and specifications that this sector demands. The coordination and execution of a specific work package regarding the manufacturing and testing samples and parts play an essential role. Therefore, the personal implication for achieving the objectives is clear, and I hope that it will be evident in the success of the CLASCO project.
Thank you to CATEC for the information.