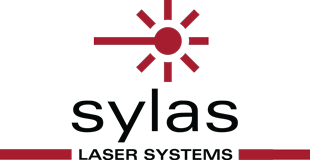
The CLASCO project – A universal and digitised laser-based post-processing method for the production of functionalised parts with complex shapes is being developed in the EU-funded CLASCO project. 12 international project partners from science, industry, research and application are united in the CLASCO project. The project is coordinated by the Technical University of Dresden. In our exclusive interview series, the CLASCO project partners introduce themselves in the areas of CLASCO Machine, Optics, Process Monitoring, Sample Preparation through Additive Manufacturing, Artificial Intelligence, Strategy and Business Model as well as Circularity and Sustainability.
Get to know the CLASCO project consortium member in the area of CLASCO Machine:
1. The main objective of the CLASCO project is to develop a universal and digitised laser-based post-processing machine to produce complex-shaped AM parts with functionalised surfaces. What is the role of Sylas Laser Systems in this project?
SYLAS SA brings its skills in laser polishing of various materials and in the design and manufacture of very high precision machines designed to work on any 3D surfaces.
2. On the way to innovative AM post-processing - what is the CLASCO Machine? What are the technical innovations and special features of the CLASCO Machine for an industrial environment?
The parts produced by Additive Manufacturing have the property to present hollows and peaks on their surfaces; in some cases, the surfaces of these parts are even porous. To make the surfaces of this type of parts functional, it is necessary to start by making them more or less smooth. To do this, there are mechanical (rework, mechanical polishing), chemical or contactless solutions (laser polishing). One of CLASCO’s innovations is to COMBINE contactless surface preparation (laser polishing) and contactless micro structuring processes in one machine in order to give them the desired functional aspects.
3. How does the SYLAS laser polishing machine fit into the broader objectives of the CLASCO project?
The CLASCO solution has two great advantages from an ecological and economic point of view:
- on the one hand, the previous ones do not pollute (no chemistry) and are not dangerous for health – indeed, all mechanical polishing processes of AM components generate microparticles which are very dangerous for health.
- on the other hand, the key processes being concentrated on a single machine, the CLASCO solution has obvious economic advantages from the point of view of equipments and production logistics.
4. What are the main challenges you foresee in the integration of laser polishing and direct laser interference patterning in a single manufacturing system?
For SYLAS, the main challenges lie in understanding and taking into account the needs of the micro-structuring process and in the differences in constraints resulting from the various degrees of quality of the surfaces to be treated: material type, initial roughness, internal impurities, …
On the other hand, we do not really expect any interference between the processes except that the internal geometrical constraints of the CLASCO machine will be relatively high.
Thank you to SYLAS Laser Systems for the information.